See What Our Customers Say
Discover why AssetWatch is the trusted choice for condition monitoring
"Once the planned maintenance strategy was operating, we saw improvements — but the next step, proactive maintenance, based on predictive maintenance and condition-based monitoring, would be where significant gains would be realized."
Real Stories, Real Transformations
“I have had great experience with my CME. We have been able to successfully repair / replace multiple gearboxes, motors, pumps, and even DC drive parts due to the info he was able to provide before the failure could cause downtime. I would recommend all plants use this service and take it seriously.”
“Very good product. User friendly installation and maintenance. Very good customer support and extremely cost effective.”
“The data results are interpreted in an understandable way which helps guide our maintenance resources.”
“With our AssetWatch® Condition Monitoring Engineer, I feel like I have a highly qualified tech on my team.”
"I’ve experienced first-hand cost avoidance in the hundreds of thousands of dollars on a furnace fan by utilizing Asset Watch and their dedicated team of SMEs. Could not recommend their services enough!"
“We don’t have enough skilled workmen, so we better have the right solution, and that’s Vero.”
"AssetWatch isn't just some monitoring system for equipment. It’s an extension of your maintenance department that comes with a highly trained team that helps grow your company. We have had a lot of other vendors try and supply a good monitoring system for different assets, but none came with the convenience of real-time, live feedback and a team of trained professionals to assist with troubleshooting, field service support, etc. This is a system I recommend for any company trying to be more preventative and less reactive."
“With the CME, I feel like I have a highly qualified tech on my team. I am not bombarded by alerts, I appreciate the conversations.”
"Great team. Great product. Paid for the first year in 2 months!"
Some Of Our Asset Saves
Explore our asset saves showing how minimal efforts can achieve maximum rewards.
Chiller Pump
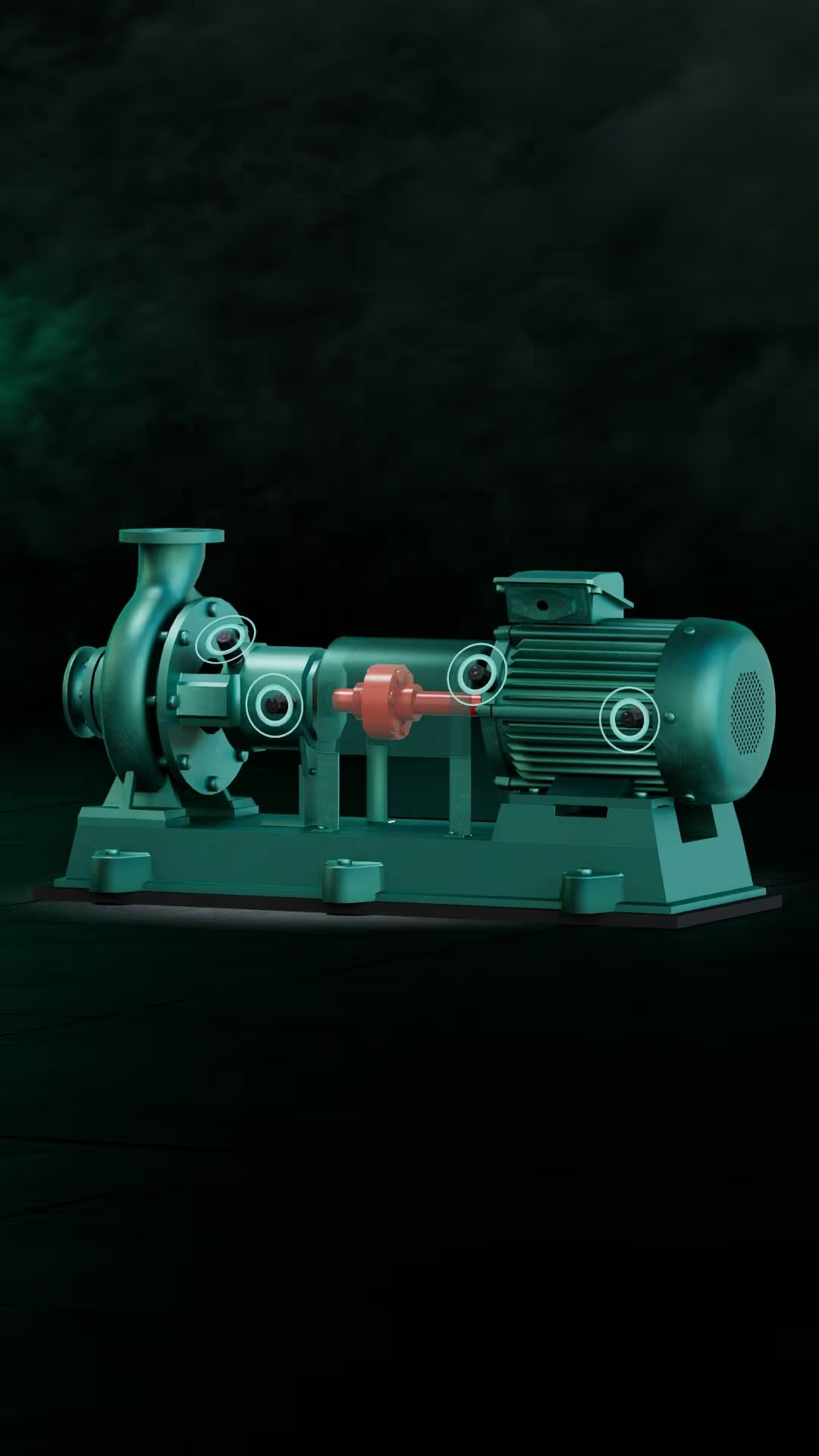
Wet Dust Collector
Wet Dust Collector
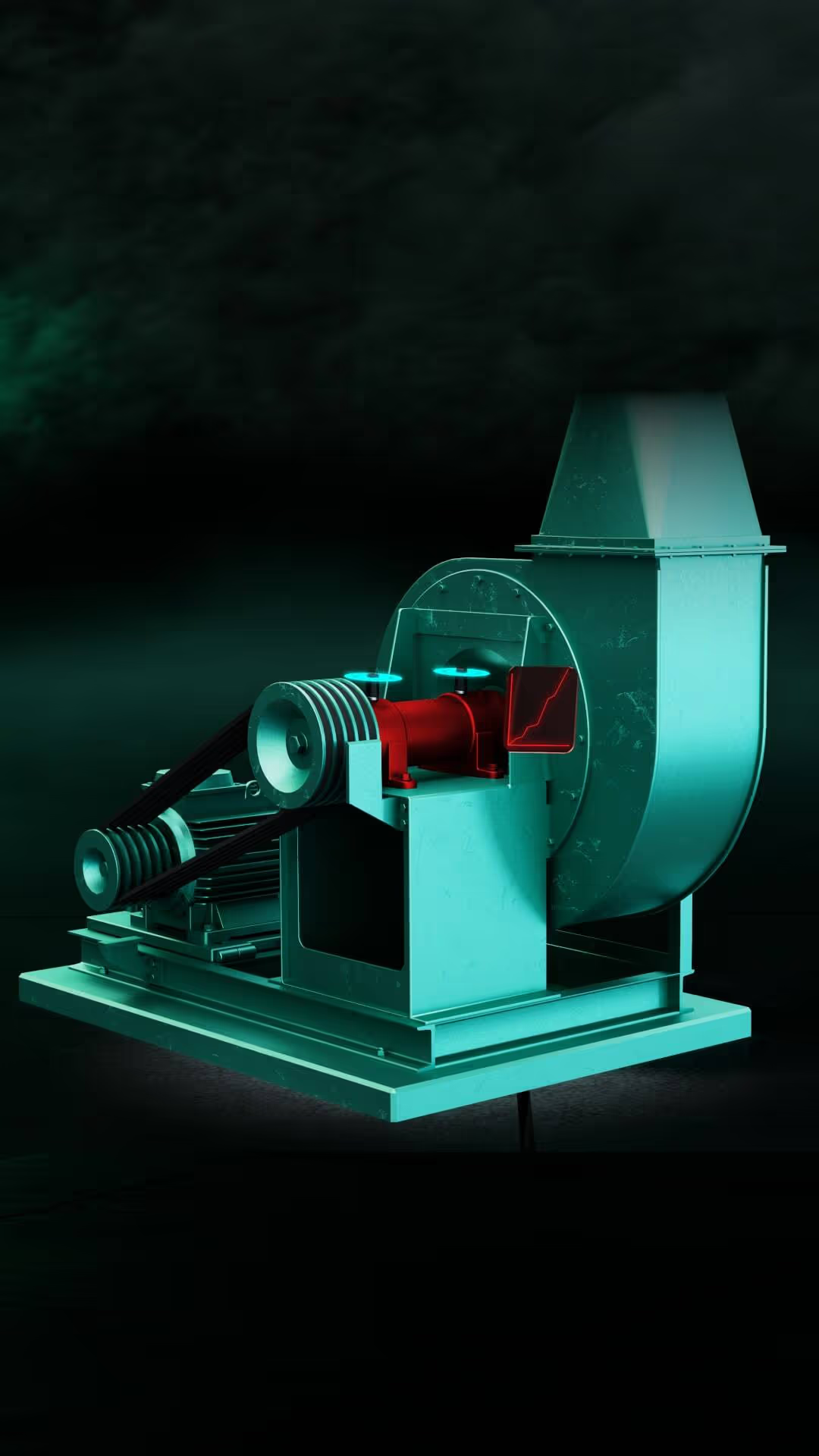
Case Studies
These teams are rockstars in their organizations and we celebrate their work.
Book a demo
Our 30-day, risk free trial is only $199.
AssetWatch customers save on average 8x in ROI. That means for every $1 you give us, we give $8 back to you.
Includes professional installation of up to 200 sensors (a $10k+ value)
24/7 monitoring and a dedicated CME for your site
AssetWatch cloud-based software with unlimited licenses
No CapEx, Engineering or IT integration required