Zero Defects
Zero defects is a quality management concept aiming for the reduction of defects and errors in manufacturing or service delivery to zero. It emphasizes continuous improvement, defect prevention, and the commitment of all employees towards maintaining high-quality standards. In maintenance, adopting a zero defects philosophy involves rigorous inspection, preventive maintenance, and a culture that prioritizes quality and continuous improvement to eliminate failures.
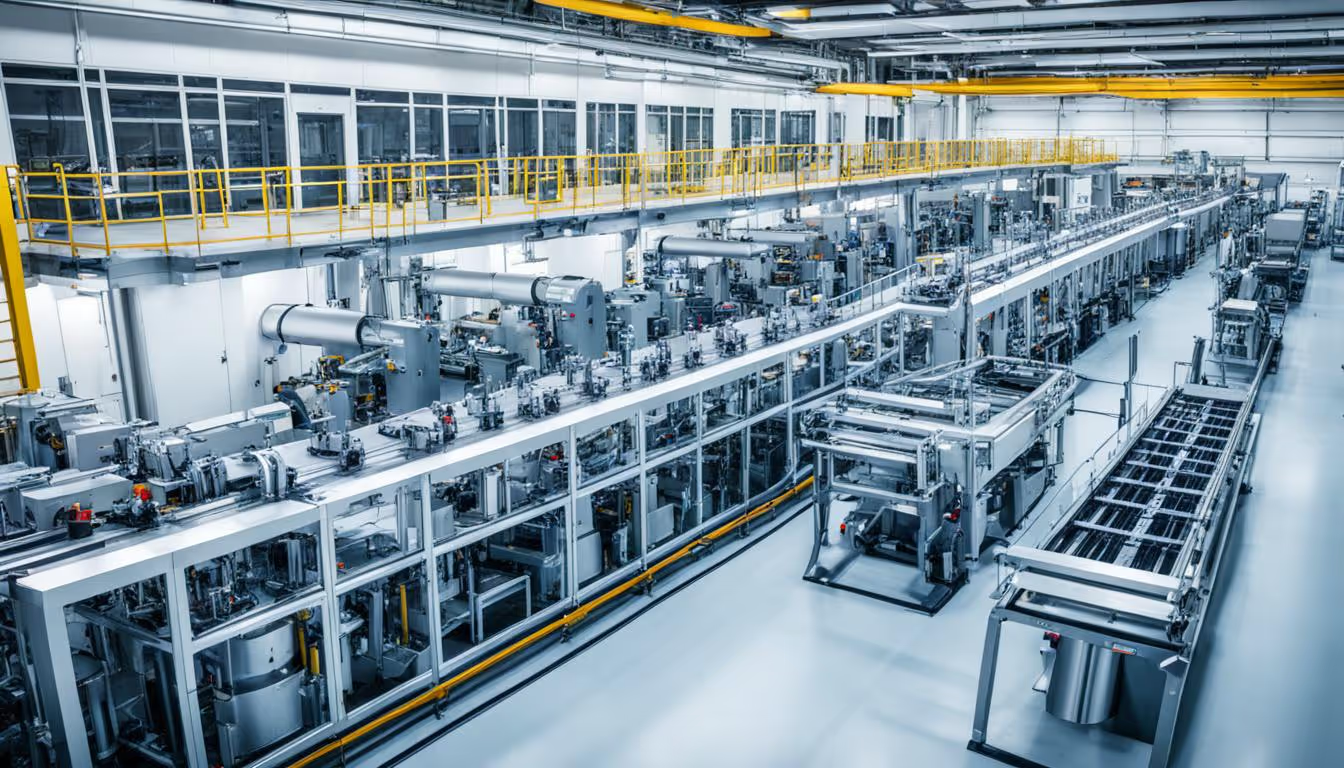
Welcome to the world of Zero Defects, where quality improvement starts with a strong focus. It aims to remove all defects in production, making it key to understand and prevent errors. This approach is inspired by quality leaders and pushes companies to own their quality standards.
It favors proactive steps over just fixing problems after they happen. This aligns with Six Sigma and Total Quality Management (TQM) strategies. By going for Zero Defects, you'll see fewer returns and happier customers. This leads to more profit and less waste.
Exploring Zero Defects means using tech like Condition Monitoring to improve. This tech gives you real-time info on your production. Join us in making your manufacturing operations more efficient and of high quality.
Key Takeaways
- Zero Defects focuses on eliminating defects to achieve quality excellence.
- The philosophy promotes proactive approaches rather than reactionary measures.
- Integration with quality management systems like Six Sigma enhances effectiveness.
- Incorporating Condition Monitoring supports real-time production insights.
Understanding Zero Defects in Manufacturing
Zero Defects is a key idea in modern manufacturing. It focuses on getting rid of defects to improve quality. This approach believes it's better to stop defects before they happen than to fix them after.
Four main ideas make up the Zero Defects method:
- Prevention: The main goal is to catch quality problems early. This way, you can make sure your products are top-notch from the start.
- Continuous Improvement: Always looking to get better is key. This keeps your processes efficient and your quality high.
- Employee Involvement: Getting your team involved is vital. It helps create a team that works together to solve quality issues.
- Commitment to Quality: Leaders must really care about Zero Defects. They need to set up policies and use resources to support it. This makes quality a big deal in your company.
Using these ideas helps you start Zero Defects in your work. It leads to making products without defects.
Implementing Zero Defects in Your Operations
Starting Zero Defects in your operations means focusing on continuous improvement and managing processes well. Begin by checking your current manufacturing processes. This helps spot areas where defects often happen.
Use data-driven methods like Vibration Analysis to find machinery issues early. These can lead to quality control problems if not caught.
It's important to set clear goals. Aim for specific, measurable goals like cutting down on defects, reducing waste, and boosting customer satisfaction scores. These goals will help guide your team and measure success.
Training your employees is key to Zero Defects success. Teach them about preventing defects and building a quality culture. Use workshops and ongoing education to focus on quality control strategies.
Using technology can improve your Zero Defects efforts. Add tools like Condition Monitoring and Predictive Maintenance to your daily work. These tools give real-time data. They help predict equipment failures, allowing for timely maintenance and better decisions.
It's crucial to keep an eye on and tweak your processes for ongoing success. Track production quality and get feedback from employees to see how well your Zero Defects efforts are working. Being adaptable ensures your strategies stay relevant to your operation's changing needs.
Zero Defects and Condition Monitoring
Using Condition Monitoring with the Zero Defects approach boosts manufacturing quality. It lets you watch equipment and the process closely in real-time. This way, you can spot problems early, keeping quality high.
Condition Monitoring uses tech like sensors and IoT devices. These tools keep an eye on machines all the time. They help you act fast if something might affect quality. This is key to predictive maintenance.
Data analytics is key to getting the most from Condition Monitoring. By looking closely at the data, you can see trends that mean a machine might break soon. This lets you fix things before they get worse, sticking to the Zero Defects goal.
Condition Monitoring helps make better decisions. Seeing how equipment is doing lets you use it wisely, cutting down on downtime. This means fewer defects and a strong focus on quality in your company. Adopting these strategies helps you aim for Zero Defects.
Benefits of Zero Defects
Using Zero Defects in manufacturing boosts your business in big ways. It leads to a huge quality jump. By focusing on stopping defects, your products meet or beat what customers want. This builds a strong reputation in your field.
Operational efficiency is another big win. With fewer defects, there's less waste and less rework. This makes your operations smoother and cuts costs. You can use the saved resources for things that add more value, making your business more productive and efficient.
Also, Zero Defects makes customers happier. Giving them products without defects builds trust and loyalty. This keeps your current customers happy and draws in new ones, leading to more sales and growth. Going for Zero Defects sets you up for long-term success. It helps you stay competitive and use resources better, which is good for the environment.