Remote Monitoring
Remote Monitoring is the process of tracking equipment's performance and condition from a distance, using sensors and network technology to transmit data to a central system or personnel. It enables the early detection of potential issues, facilitates predictive maintenance, and reduces the need for on-site inspections, thereby saving time and resources. Remote monitoring is particularly valuable for managing assets in difficult-to-access locations or across multiple sites.
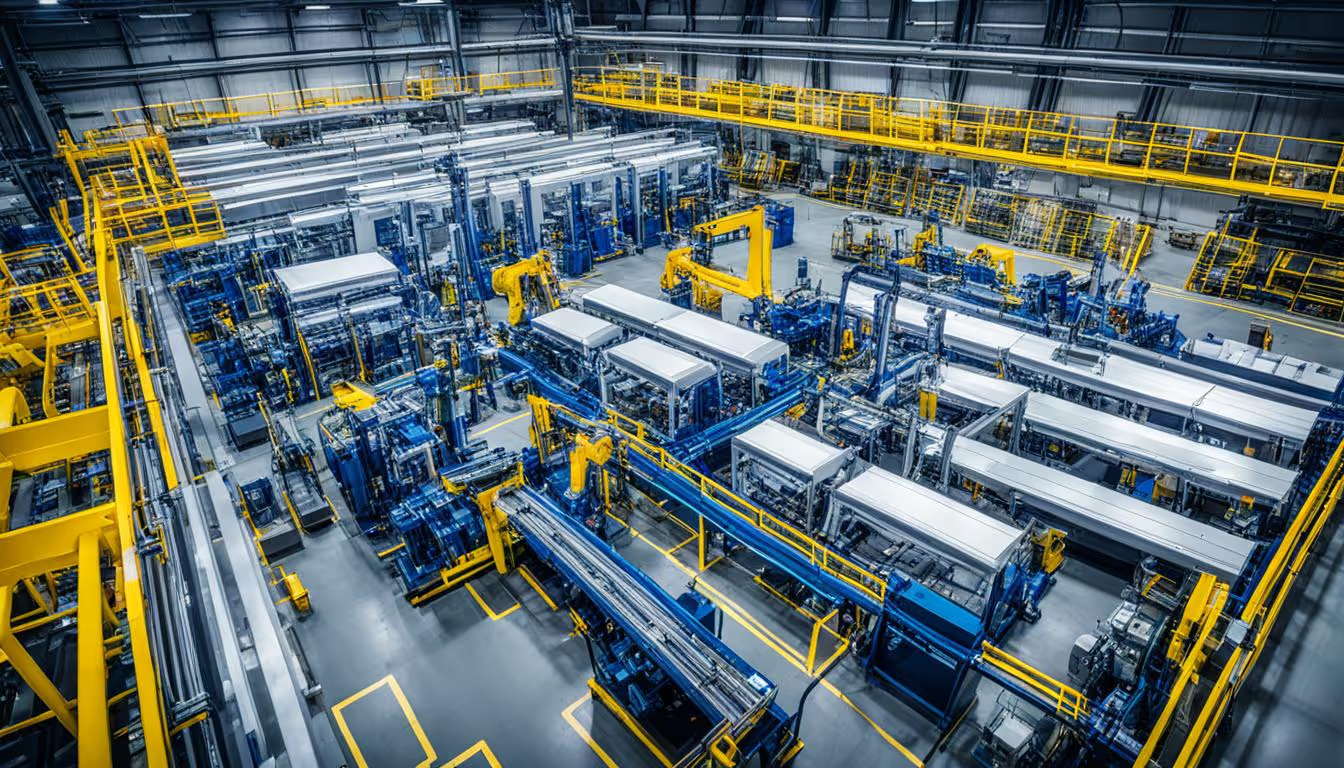
Remote Monitoring in Manufacturing
In today's fast-paced manufacturing world, Remote Monitoring is key for businesses wanting to boost efficiency. By using IoT devices and cloud systems, you can watch over your manufacturing in real-time from anywhere. This new way of working includes Condition Monitoring to keep an eye on equipment health. It also helps with Predictive Maintenance plans.
With asset remote monitoring, you can spot equipment failures before they happen. This cuts down on maintenance costs and makes your equipment last longer. It shows how important digital changes are in manufacturing today.
Visualize a manufacturing plant with a bird's eye view, where a large number of machines and equipment are working in sync. Show how an operator is able to monitor their performance remotely through a digital dashboard displayed on a tablet. The dashboard should display real-time metrics, such as production rate, downtime events, and maintenance needs, giving the operator full visibility over the entire manufacturing process. In the background, show a large screen displaying analytics and insights generated by the monitoring system to improve overall efficiency and productivity.
What is Remote Monitoring in Manufacturing?
Remote Monitoring in Manufacturing uses tech to watch over production from afar. It uses cloud platforms to gather data, giving you insights into how things are running. IoT devices send real-time data, helping you understand what's happening.
Vibration Analysis is a key part of Remote Monitoring. It checks the health of mechanical systems by looking at vibrations. This way, you can fix problems before they slow down production.
Remote Monitoring also gives you Prescriptive Insights. These are tips based on the data you collect. They help you make smart choices quickly, keeping your production smooth.
Also, Preventative Maintenance gets a big boost from constant monitoring. By knowing how systems work over time, you can plan maintenance before things break. This means less downtime and more production.
Benefits of Remote Monitoring
Using Remote Monitoring in manufacturing brings many benefits that can change how you work. It lets you collect and analyze data in real-time. This makes your manufacturing processes much more efficient.
Predictive Maintenance is key to this change. It helps spot equipment problems early. Fixing these issues before they get worse means less unexpected downtime. This boosts productivity in your operations.
Asset remote monitoring keeps an eye on your operations all the time. This lets you use resources better and cuts costs. You can make smart choices by knowing what's happening with every part of your operations.
Remote Monitoring also helps you work better. It helps you make workflows better, increase what you can make, and cut waste. Focusing on what's important in manufacturing helps you grow and get better.
- Real-time data collection supports quick decision-making
- Improved equipment reliability through Predictive Maintenance
- Optimized resource allocation leads to cost savings
- Minimized waste and increased production efficiency
Implementing Remote Monitoring Solutions
Starting to use Remote Monitoring Solutions in your factory needs a strategic integration of tech and processes. First, look at your current workflows to see where asset remote monitoring can help the most. Checking equipment health and performance can show you where condition monitoring is most useful.
Once you know where to focus, pick the right tech that meets your goals. Make sure these systems work well with condition monitoring to boost your remote monitoring efforts. Various companies can guide you on the best tech for your factory.
But, success isn't just about the tech; it's also about your team. Training your staff is key to using remote monitoring tools well. They need to be sure about how to use these systems and understand the data they give.