Ready Line
In military and aviation contexts, the ready line refers to a designated area where aircraft or vehicles are positioned fully serviced, armed, and ready for immediate use. In broader maintenance terms, it can refer to equipment or machinery that is fully operational and available for deployment or production, emphasizing the importance of maintenance in keeping critical assets in a state of readiness.
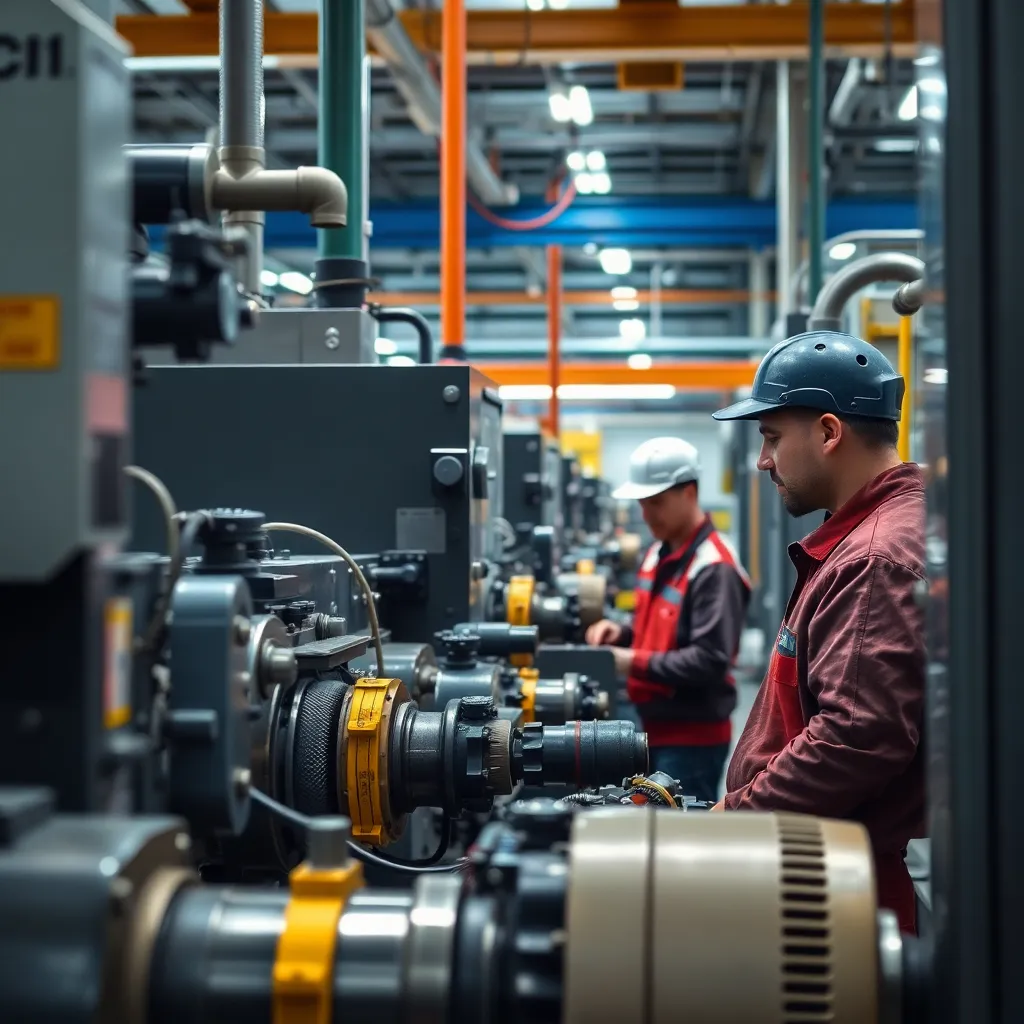
Key Takeaways
- Ready Line signifies the operational readiness of equipment in maintenance.
- It involves proactive strategies like predictive maintenance and condition monitoring.
- Preventative maintenance is essential for maintaining the Ready Line.
- The concept encourages a holistic approach to equipment management.
Ready Line refers to the operational readiness of equipment or machinery within a maintenance framework. This term is vital for organizations aiming to optimize their maintenance processes and ensure minimal downtime. In the maintenance industry, the idea of a Ready Line embodies a proactive approach, emphasizing the need for machinery to be consistently prepared for operation. By maintaining a high level of readiness, businesses can improve operational efficiency, reduce unexpected failures, and enhance productivity.
Incorporating predictive maintenance practices into the Ready Line concept is crucial. Predictive maintenance utilizes data-driven insights to forecast when a machine may require maintenance, allowing for timely interventions before issues arise. This proactive methodology, alongside condition monitoring, enables technicians to assess the real-time status of equipment, ensuring that the Ready Line remains intact. Furthermore, preventative maintenance complements these strategies by scheduling regular upkeep and inspections, thereby reinforcing the overall reliability of machinery.
Common misconceptions about the Ready Line include the belief that it solely focuses on reactive measures or the idea that maintenance is merely a checklist of tasks. In reality, the Ready Line emphasizes a holistic approach to equipment management, integrating ongoing evaluations and data analytics. By adopting these principles, organizations can avoid costly downtimes and foster a culture of continuous improvement.