Operational Efficiency
Operational Efficiency refers to the ability of an organization to deliver products or services in the most cost-effective manner while ensuring quality and customer satisfaction. In maintenance, improving operational efficiency involves optimizing maintenance processes, reducing downtime, and ensuring equipment runs at peak performance. Strategies include implementing preventive maintenance, leveraging technology, and streamlining workflows.
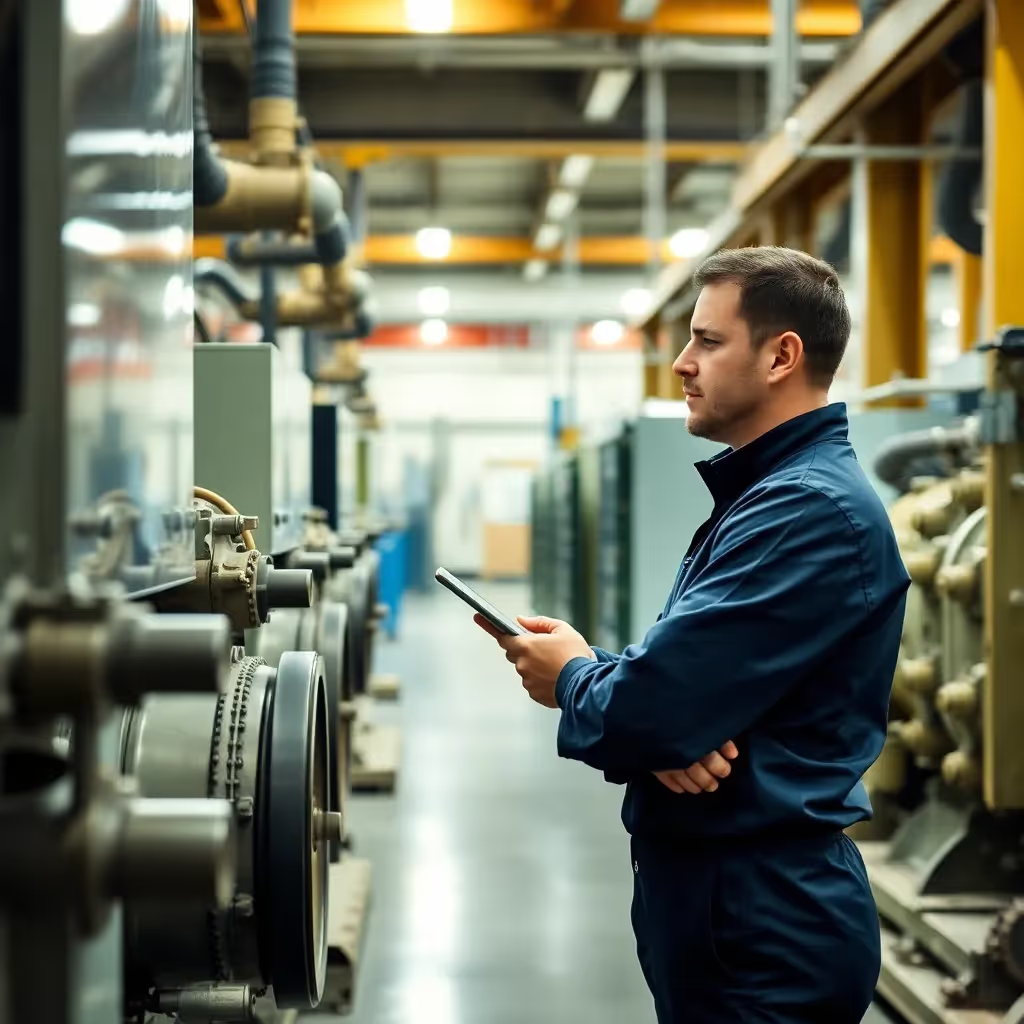
Key Takeaways:
- Operational efficiency minimizes downtime and reduces costs in the maintenance industry.
- Condition monitoring plays a vital role in transitioning to preventive and predictive maintenance strategies.
- Initial investment in advanced monitoring systems can lead to significant long-term savings.
- Understanding the relationship between maintenance practices and operational efficiency is crucial for organizational success.
Operational Efficiency refers to the ability of an organization to deliver products or services to its customers in the most cost-effective manner without compromising quality. In the maintenance industry, achieving operational efficiency is crucial as it minimizes downtime, reduces operational costs, and enhances the overall effectiveness of maintenance strategies. By streamlining processes and utilizing advanced technologies, organizations can improve their operational workflows and significantly increase their productivity.
One key aspect of operational efficiency in maintenance is Condition Monitoring. This strategy involves continuously assessing the health of equipment through various techniques, such as vibration analysis, to identify potential issues before they lead to equipment failures. By integrating condition monitoring into maintenance practices, organizations can transition from reactive to preventive maintenance, ultimately fostering better operational efficiencies. Additionally, this proactive approach aligns with Predictive Maintenance, where data analytics and real-time monitoring are employed to forecast equipment failures, allowing for timely interventions and optimized resource allocation.
In the realm of operational efficiency, misconceptions often arise regarding the perceived costs associated with implementing condition monitoring and preventive maintenance systems. While initial investments may seem high, the long-term savings derived from reduced downtime and maintenance costs significantly outweigh these expenses. For instance, industries that have adopted predictive maintenance practices report decreased maintenance costs by up to 30% and increased equipment life by 20%.
Operational efficiency is an essential concept within the broader field of maintenance management, where best practices involve continuous improvement and adaptation of maintenance strategies to enhance productivity and reduce costs. The integration of modern technologies and methodologies ensures that organizations remain competitive and responsive to the ever-evolving demands of the industry.