
Furnace roll bearing save prevents $500k loss and averts 48 hours of downtime.
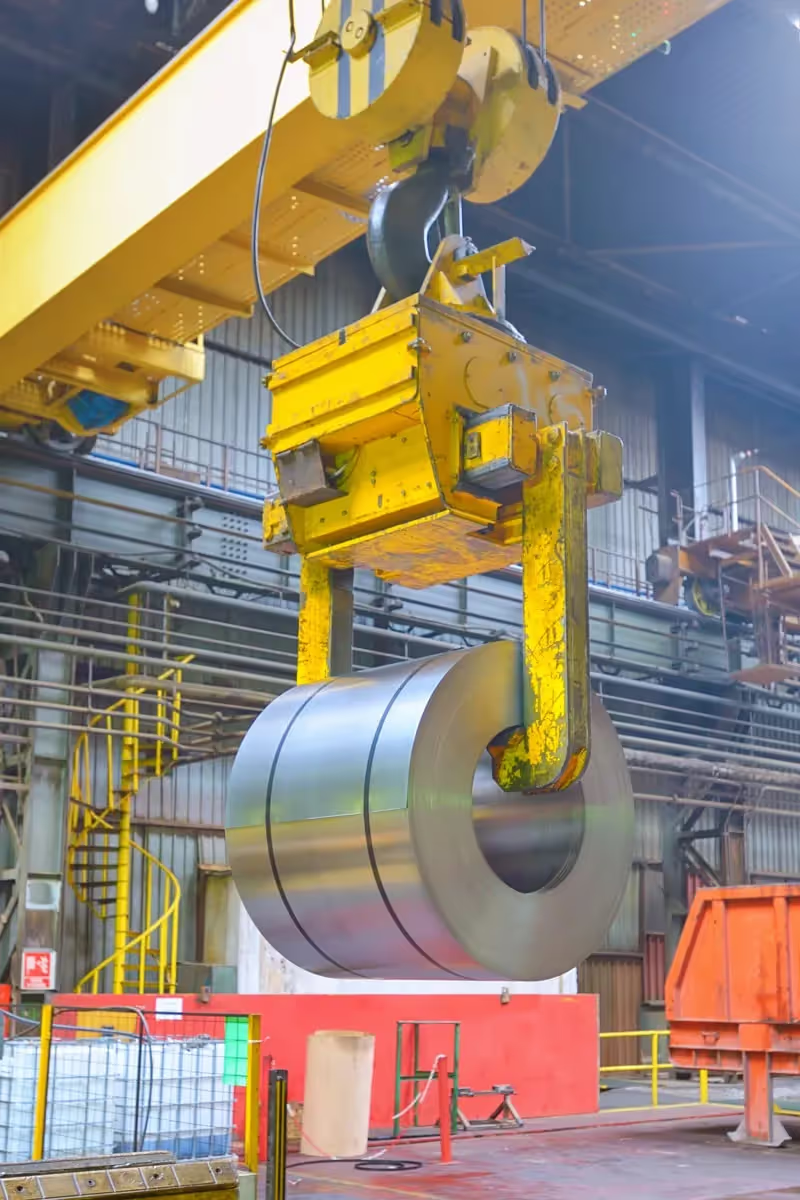
The Challenge
Unplanned downtime destroys profitability in continuous process manufacturing. In their quest for operational excellence, Worthington Steel searched for a remote condition monitoring solution to reduce machine failures and increase uptime at their Toledo hot-dipped galvanizing facility. The steel processor implemented Vero® across the plant and realized an 18% decrease of machine-related downtime and a 17% reduction in reworks.
Creating Value, Resolving Issues
The Worthington Steel Delta Galvanizing Plant, located near Toledo, is a clear example of how machine health insights can drive proactive maintenance and deliver stellar returns.
Within weeks of installing Vero®, the early detection of a furnace roll bearing failure by the AssetWatch® Condition Monitoring Engineer (CME) allowed for the planning of its replacement on a down-day. The bearing vibration was undetectable by naked ear and touch.
If this bearing had failed during a line run, it would have caused approximately 48 hours of unplanned downtime and potentially $500k in lost gross margin.
Below are the results from the first six months of Vero® service at the facility.
Jeremie Lieb Maintenance Agile Team Lead
Condition based monitoring in action
Within weeks of installation, the Delta Plant we had a HUGE win with early failure detection and proactive, planned replacement of a furnace roll bearing, preventing approximately 48 hours of unplanned downtime and potentially $500k in lost gross margin.
One Sensor Saved a Potential $500k in Lost Gross Margin!
Get Started TodayFind this case study helpful? We’d love to share it with you!
AssetWatch partnered with AWS to provide the scalability and reliability needed to support a serverless architecture. With a robust suite of services tailored for data ingestion, processing, and machine learning, AWS enables AssetWatch to seamlessly scale sensor data and deliver predictive insights to manufacturing companies. AWS infrastructure reduces operational overhead and allows AssetWatch to focus on innovation to drive value to our customers. Additionally, AWS’s strong security framework and global infrastructure ensure the resilience and compliance required to support mission-critical manufacturing operations at scale. This partnership positions AssetWatch to accelerate growth while maintaining the highest levels of performance and reliability.
.avif)

One Sensor Saved a Potential $500k in Lost Gross Margin!
Enterprise Results
After initially deploying Vero® at its flagship steel processing facility in Columbus, OH, Worthington Steel expanded the proactive maintenance system across their enterprise. In total, more than 1,800 vibration+temperature sensors are now tracking the health of 650+ critical machine assets at 17 steel processing and pressure cylinder facilities located throughout North America.
Since the first installation, more than eight million full-spectrum vibration and temperature readings have been gathered by Vero® sensors and delivered to AssetWatch® for processing and visualization on its cloud-based software platform. Assisted by machine learning, expert Condition Monitoring Engineers (CMEs) have analyzed the data and have issued more than 400 prescriptive maintenance recommendations.
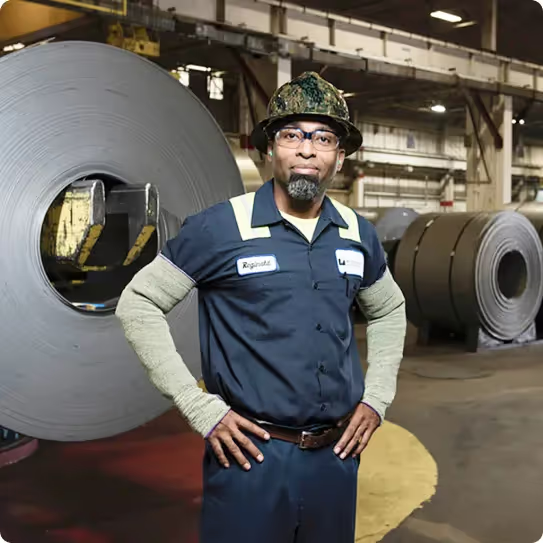
“Worthington Steel is a global leader in its field, but we needed a solution that was outside our purview. We sought out a partner that had specialized expertise.”
Brad Kern, VP, Steel Operations
Our 30-day, risk free trial is only $199.
AssetWatch customers save on average 8x in ROI. That means for every $1 you give us, we give $8 back to you.
Includes professional installation of up to 200 sensors (a $10k+ value)
24/7 monitoring and a dedicated CME for your site
AssetWatch cloud-based software with unlimited licenses
No CapEx, Engineering or IT integration required