Innovative AI-Powered Monitoring: Preserving Air Quality and Elevating Performance at Baghouses
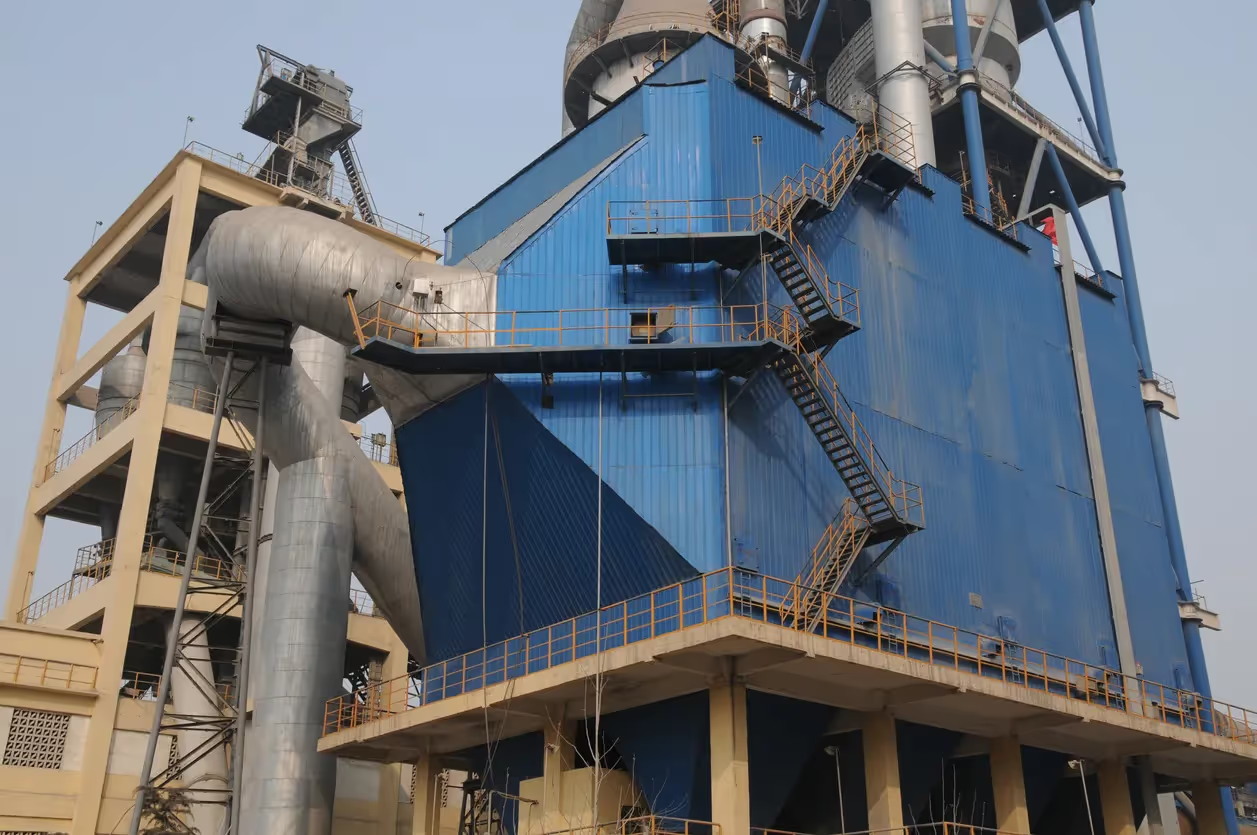
The Challenge
Maintaining baghouse performance is crucial for air quality control in power plants, steel mills, aluminum mills, mining, cement plants, chemical manufacturing, food processing, and grain milling. Unchecked, equipment wear and failure can lead to significant operational disruptions, environmental releases, and regulatory fines.
Catastrophic Fan Failure Avoided
Alerted by AI, the AssetWatch Condition Monitoring Engineer (CME) monitoring machine health for a steel mill observed a baghouse fan ODE showing several harmonics of 1x fan speed, indicating rotating looseness, and time wave form showing high amplitude (>50g's Pk-Pk) impacting spaced at 1x fan speed. The CME issued a Maintenance Recommendation and notified the customer to check the fan bearings for excessive clearance by conducting a shaft lift check or measuring bearing clearances.
The lift test confirmed 0.019"-0.020" excessive wear (0.025" overall). After disassembly, it was discovered that the bearing was damaged and the housing was worn. Both were changed and vibration amplitude decreased from >50 g's to 4.5 g's Pk-Pk, avoiding a catastrophic failure. The customer estimated that 24 hours of downtime were prevented and cost savings of more than $58k.
AssetWatch Expert
Maximizing Returns: AssetWatch's Impact on Baghouse Operations
AssetWatch's innovative AI solution not only enhances operational efficiency but also significantly cuts down costs. By reducing downtime and maintenance expenses, AssetWatch ensures a substantial return on investment for baghouses.
AssetWatch's AI reduced vibration by 77%, extending asset life
Get Started TodayFind this case study helpful? We’d love to share it with you!
AssetWatch partnered with AWS to provide the scalability and reliability needed to support a serverless architecture. With a robust suite of services tailored for data ingestion, processing, and machine learning, AWS enables AssetWatch to seamlessly scale sensor data and deliver predictive insights to manufacturing companies. AWS infrastructure reduces operational overhead and allows AssetWatch to focus on innovation to drive value to our customers. Additionally, AWS’s strong security framework and global infrastructure ensure the resilience and compliance required to support mission-critical manufacturing operations at scale. This partnership positions AssetWatch to accelerate growth while maintaining the highest levels of performance and reliability.
.avif)
